Moving the Tagger Microscope
Moving the Tagger Microscope Along the Focal Plane
Tagger Microscope
- Prior to Installation in the Tagger Hall
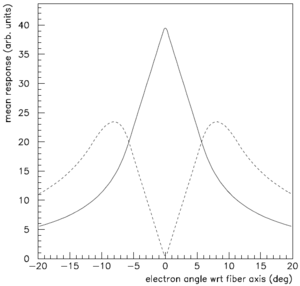
The tagger microscope (TAGM) consists of six major components: upper enclosure, lower enclosure, optical fibers, electronics, shielding, and darkening shroud. As seen from the CAD image above, Figure 1, the lower enclosure houses the microscope's electronics, while the upper enclosure contains the optical fiber bundle supports (a.k.a. popsicle sticks). The bundle supports are used to align the scintillating fiber (SciFi) longitudinal axis to the incoming electron's path angle as it passes through the tagger magnet's focal plane. The designed angular tolerance, e.g. fiber to electron allowable angular error, is < 0.5o. MC simulations were performed to test the effect of various amounts of misalignment between the electron angle and the SciFi axis. Figure 4 shows a plot of one of these simulations with the solid line showing the scintillation response of the central fiber, while the dashed lines are the response for the adjacent fibers. A factor of three separation between adjacent signal amplitudes is achievable when alignment is < 3o. In order to achieve optimal alignment, similar to < 0.2o that was seen in bench tests, the SciFi end of the optical fibers are affixed to bundle supports (Figure 5) in the upper enclosure, with the light guide potion of the fiber extending down to silicon photomultipliers (SiPMs) located on preamplifier boards (Figure 6) in the lower enclosure.
- The two ends of the optical fibers
Moving the TAGM to a new energy range not only involves the physical relocation of the microscope and its shielding along the tagger magnet's focal plane, but also requires internal realignment of the fiber, which is the subject of this page. The realignment of the scintillating fibers' longitudinal axes requires all 17 bundle supports to have new, individual crossing angles (β angle) with respect to the focal plane. These angles are derived from a table generated based on a TOSCA map of the post-bremsstrahlung electrons' crossing angles as they pass through the magnet's focal plane. Since the crossing angle changes with energy (e.g. displacement along the focal plane) each bundle support will have a slight "kick" or "tow" from the adjacent bundle support. The tow is typically on the order of 0.1o.
Since the bundle supports have varying β angles, the parallel railing system that holds these supports in place are no longer representative of their namesake. That is, the front and rear rails of the parallel railing system are not parallel to each other and have a pitch with respect to one another. Figure 7 is a pictorial explanation of this and shows that for two equal length rails (front & rear), the length of the upstream and downstream alignment bars differ by 0.039 ± 0.001 in. at a starting photon energy (Eγ) with a required tow of 0.09o between bundle supports. For each individual photon energy range covered by the microscope, or more simply stated for each energy that the microscope starts at, a new pitch for the parallel rails must be determined and three components (upstream alignment bar, downstream alignment bar, and upstream guide plate) unique to that starting energy must be fabricated. For this reason CAD drawings, an Excel spreadsheet, and this wiki page were created to provide the information needed to realign and move the TAGM to any starting photon energy between 11 and 5 GeV. The turnaround time for the machining components is typically five to seven days, while the realignment of fibers will take no more than two days with inexperienced workers.
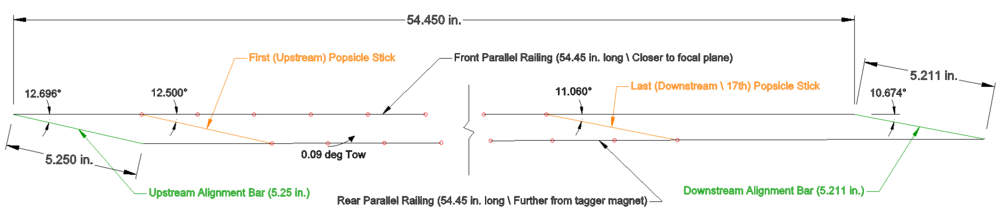
Coordinate System
There are three coordinate systems often referred to inside the GlueX Tagger Hall. These coordinate systems have origins associated with the Goniometer center (room coordinates), Tagger Magnet center (map coordinates), and the focal plane (FP coordinates). The room coordinate system has the positive z-coordinate along the beam axis with the positive y direction pointing to the ceiling of the tagger hall from the coordinates origin placed at the Goniometer's center, where the beamline radiator is located. Figure 1 shown below, taken from a presentation by Dan Sober, shows the three coordinate systems relative to one another. The map coordinate system (magnetic mapping) places the y-coordinate along the long axis of the magnet with the positive x-axis parallel to the tagger hall floor in the direction of the focal plane. the positive z-axis of the map coordinate system points toward the tagger hall ceiling. When viewed from above the map y-coordinate is offset from the room coordinate z-axis by 6.5 degrees towards the focal plane (clockwise). The focal plane coordinate system places its x-axis along the electron focal plane with zero being at an electron energy equivalent to a photon energy around 11.7 GeV. The positive x-axis points toward increasing electron energy (decreasing photon energy). The positive y-axis of the focal plane coordinate system points towards the tagger magnet and is parallel to the tagger hall floor. This leaves the focal plane positive z-axis pointing towards the tagger hall ceiling.
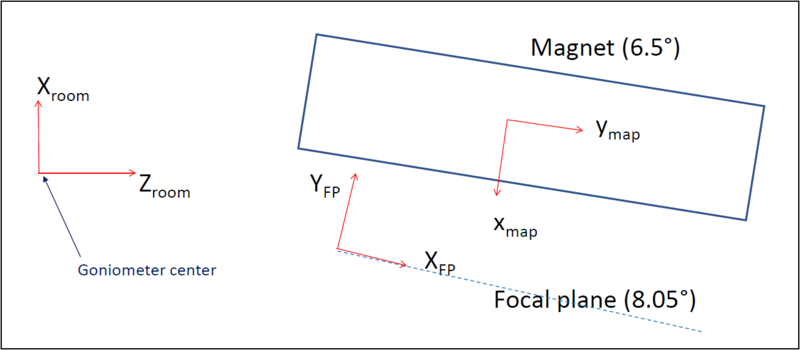
In Spring 2017 a survey of the various beamline components saw a small change in the Tagger Microscope position. The Microscope (upstream center) position derived from this survey is shown below and includes a magnet center shift from previous measurements.
|
|||||||
X room = | - 1.16666 m | ||||||
Z room = | 7.41009 m | ||||||
Angle room = | - 8.05220o |
|
|||||
Xmap = | 0.73488 m | ||||
Ymap = | 1.22645 m | ||||
XFP = | 3.31245 m | ||||
YFP = | -0.00932 m |
|
|||||||
XFP = | 3.26198 m | ||||||
YFP = | 0.0 m | ||||||
Eγ = | 9.201 GeV | ||||||
β = | 12.695o |
Bundle Support (a.k.a. Popsicle Stick)
The Tagger Microscope (TAGM) contains 17 optical fiber bundle, each consists of a 5x6 array of 30 fibers for a total of 510 fibers (5 rows, 102 columns). Figure 2 below shows the fiber array as viewed by the electrons passing through the tagger magnet focal plane. Each optical fiber consists of a 2 mm2 x 2 cm BCF-20 scintillating fiber (SciFi) thermally fused to 2 mm2 x 165 cm BCF-98 light guide, see Figures 3 & 4. The SciFi end of each fiber is thermally bent into an "S" shape to remove the fiber from the electrons' path soon after passing through the SciFi, see Figure 5. The fiber begins its bend out of the electrons' path after only 4.5 cm. This length provides enough material past the fused joint to minimize strain on the joint resulting from the bend and fiber mounting straps, while also reducing the material in the line-of-fire that could result in backscatter.
- Transmission of scintillation light
- Bundle Support for a 5x6 Array of Fibers
Popsicle Stick Limitations
Placing the "Pivot Point" on the focal plane and only allowing +0.5 cm towards the tagger magnet the maximum crossing angle for the current bundle support design is βmax = 19.51o, while the minimum angle is βmin = 4.05o. This does not account for the most forward bundle mounting strap clamp and bolts, but they are lower in ZFP than the fibers and should not extend significantly past the 0.5 cm limit even at lower β angles.
Calculating Position of Each Bundle Support Mounting Rod
Up to 17 bundle supports can be mounted on the parallel railing system and instrumented in the TAGM. As the range of photon energies being tagged decreases (e.g. electron energy increases) the crossing angle (β angle) of the electrons with the focal plane also decreases. The smaller the β angle the more space along the XFP axis a bundle support will occupy. Below an Eγ of 6.5 GeV (β = 9.5o) the length of the parallel railing system can only mount a maximum of 16 bundle supports.
Since the β angle changes across the TAGM energy range, a universal bundle support β angle cannot be used. Starting with the most upstream bundle support (e.g. highest energy tagged photons) an initial bundle support angle is selected by taking the average of the crossing angles at the tagger magnet's focal plane for the electrons that pass through the center of the first and sixth fiber columns of that bundle. Recall that each bundle support holds an array of 5x6 fibers split into two 5x3 bundle halves. These halves are offset so that the bundle "pivot point" and the front center of each bundle half will all sit on the focal plane for β = 12o. The pivot point is located at the midpoint of the bundle halves' offset and the boundary point of the two bundle halves (e.g. along the bundle support long axis). The long axis, which lies along the bundle support centerline, passes through the pivot point, front mounting rod, and rear mounting rod. This fact is exploited during the calculations to follow. The pivot point is solely determined from the bundle support's design (e.g. offset distance) and is essential for fiber alignment on the focal plane. Regardless of the bundle β angle, if the focal plane passes through the bundle support's pivot point then the SciFi's will be at their optimal location with the magnitude of maximum fiber extension (± YFP) being the same.
Once the β angle for the first (upstream) bundle support is set, derived from the the starting photon tag energy, each subsequent bundle support has a β angle offset from the previous one by a tow angle. Thus, as we look downstream from one bundle support to the next, the β angles differ by -(tow angle). Adjacent bundle supports will come in contact with one another at the SciFi end and form a triangular gap along their adjacent sides based on the tow angle.
An Excel spreadsheet has been created to calculate the location of the bundle supports' mounting rods with respect to the focal plane coordinate system. This spreadsheet also calculates the length of the parallel railing end supports which need to be fabricated anew for each unique TAGM location on the focal plane. One last, but very important thing that the spreadsheet calculates is the shim size needed, during TAGM realignment, in order to achieve the proper tow angle between bundle supports during mounting. In addition to the spreadsheet, an AutoCAD drawing used to design the three parallel rail components needed for each unique tagging energy spectrum starting position of the TAGM and a drawing for the current setup (β = 12.5o to 11.06o). These files are in US standard units (inches) and to scale with a tolerance of ± 0.001 inch.
A summary of the spreadsheet calculations is on the following wiki page:
TAGM Move Parameters for various Eγ Starting Points
Using the calculations explained in "Calculating the move" wiki page, the following parameters for a 6 GeV maximum tagged photon energy were determined.
|
|